On March 21st, the "International Industry Forum on Technologies and Future Applications Trend of Wide Bandgap Components, " was jointly organized by the Industrial Bureau of the Ministry of Economic Affairs and EETimes at the HNBK International Convention Center. DEKRA iST was invited to share Operating Reliability Validation and Dynamic Measurement Methodology of Wide Bandgap Power Devices. The venue was filled to capacity, with a captivated audience attentively listening to discussions about the validation technology trends of wide bandgap power devices.
Max Chen, Senior Manager of the Component Engineering Department at DEKRA iST, opened the discussion by outlining the four main points covered in today's presentation:
- The reliability requirements for power components by automakers;
- The disparities between static and dynamic reliability;
- The pivotal dynamic reliability test: IOL (Intermittent Operating Life) testing;
- The significance of an integrated technology platform of static and dynamic measurement.
Max Chen has noticed a significant surge in the use of power components in the automative industry, especially in electric vehicles, where the number of these components has skyrocketed by 7 to 10 times compared to traditional internal combustion engine vehicles. With this rise, however, comes an increased risk of failure. In order to meet stringent safety standards, automotive manufacturers are requiring the failure rate to be measured by PPB (parts-per-billion) level, and striving for nothing short of perfection with Zero defect. As a result, effectively validating the reliability of these components has become a burning topic of concern for suppliers of wide bandgap power components.
Max Chen highlighted that in the automotive electronics domain, apart from the specific standards set by each OEM, there are three major international standards governing automotive semiconductors, modules, and even system components: the AEC Q-series, AQG324, and ISO16750. It's worth noting that these standards for automotive electronic applications are closely interconnected. Therefore, when reliability testing is developed, it is crucial to consider testing requirements from head to toe, from upstream components to downstream modules/systems.

Max Chen added that automotive power semiconductors should be produced in accordance with the AEC-Q101 requirements. It is only when the products are declared to be compliant with the AEC standard after testing that the products can satisfy the basic requirements of OEMs. AQG324, on the other hand, outlines the testing protocols specifically designed for power modules. Automotive manufacturers often request testing data from suppliers because several test parameters are closely aligned with the evaluation of the lifetime of power modules. Additionally, ISO 16750 is in place for validating the reliability of Electronic Control Units (ECUs) or subsystems.
Max Chen went on to point out that the emerging WBG technology has enabled faster switching operations but also introduced new failure mechanisms. He elaborated on the differences between static and dynamic testing and provided concrete examples of testing validation.
In response to the current trend of WBG semiconductors advancing towards voltages exceeding 1200V, High-V (Voltage) H³TRB is employed for testing. It is recognized that conventional voltage inputs for validation no longer fits the real-world EV applications. Furthermore, there is a growing demand from end customers in the market for component suppliers to extend testing durations to 2,000 hours, 3,000 hours, or even longer. The purpose is to demonstrate the reliability and lifetime of the products by testing them under harsh conditions.
Max Chen elaborated further that since high-frequency switch mode power supplies have been considered the top choice for most applications, standards are now evolving to define testing methodologies tailored to dynamic reliability. For example, Dynamic H³TRB/DRB (Dynamic Reverse Bias) introduces dynamic bias under humid conditions, while Dynamic Gate Stress ( DGS ) applies pressure to the gate through voltage variations, where drift values of Vth and RDS (on) can be rendered. That is to say, “detecting hidden issues within the switching components requires meaningful data obtained” through testing of dynamic performance, which involves simulation of the actual product environment. By assessing four key indicators of MOSFET dynamic performance—switching losses, time, overshoot, and switching speed—we can effectively anticipate and address potential challenges associated with high-frequency switching.
What’s more, IOL (Intermittent Operating Life) testing is also a critical test item in the automotive field. It primarily examines the temperature cycling of devices due to self-generated heating power. Cycling the devices on and off for a long period replicates the typical field conditions. The components are self-heated by applying power until a predefined junction temperature is reached, and power is subsequently removed to cool the device back to ambient. This process is complemented by thermal imaging to observe temperature increases and detect abnormal leakage current. In addition to integrating heat and electricity, the IOL testing also entails prior measurement of thermal resistance (Rth) based on the product's structure and future assembly pattern to control junction temperature. Only by simulating the real-world conditions for product use can we collect more reliable reference data and effectively detect potential issues of the product structure. Besides, DEKRA iST even devises a platform that includes DPT Test, SC Test, UIS Test, and Short Circuit Test for dynamic measurement. The test data from the platform is made available to customers or the industry for reference.
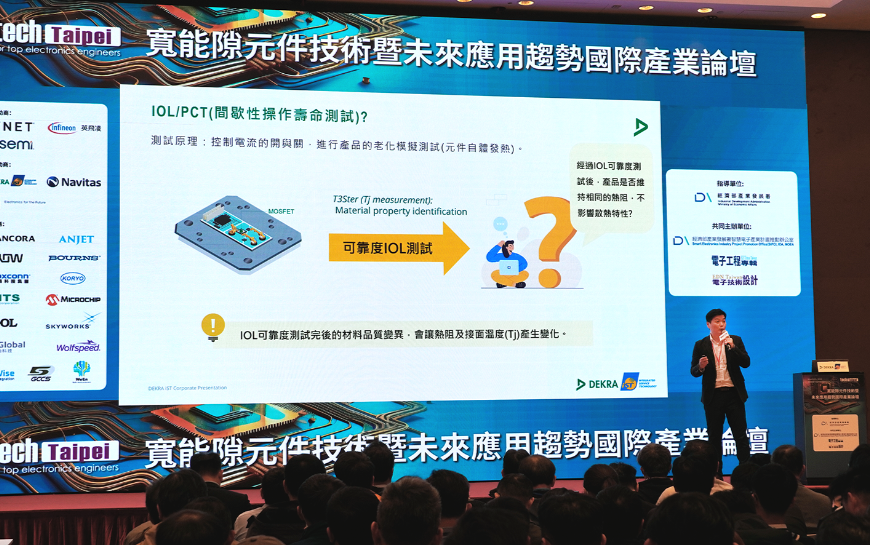
On another note, the combination of power and heat allows us to simulate data for the Safe Operating Area (SOA). We make use of static measurements and thermal resistance measurement apparatus to respectively acquire electrical parameters, such as RDS(ON)/VDSS/IDS(Max-Pulse) and thermal characteristics parameters, like Design Tj-max/Rth-jc/Pulse Zth. We are able to define the safe operating area of the components from the both parameters, making sure that the product operates within a safe area. Moving on, we evaluate the real test results of the components through Functional Testing (FT) before and after reliability testing. Then, we crosses check our results with those of other laboratories to ensure consistency. Such comprehensive testing plays an essential role in identifying potential issues and providing reliable solutions to our customers.
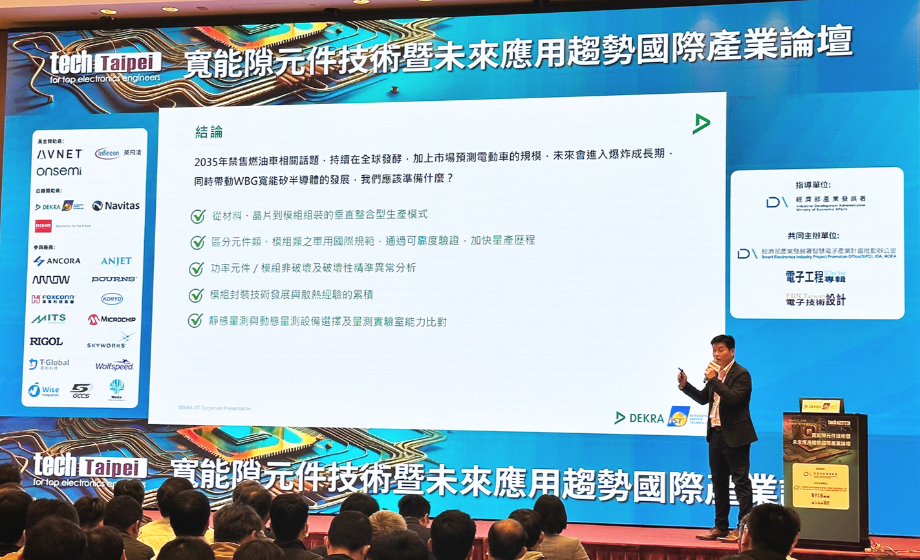
Max Chen concluded five key areas for industry leaders to consider amidst the global shift towards zero-carbon emissions and the phasing out of petrol cars:
- Establishing a vertical integrated production model from materials, chips to module assembly;
- Differentiating international automotive standards of components and modules and shortening mass production journey through reliability testing;
- Conducting nondestructive and destructive tests on power components/ modules to precisely analyze product defects;
- Developing module assembly technology and accumulating dissipation experiences;
- Selecting both static and dynamic measurement equipment and comparing lab capacities.
To excel in the electric vehicle market, power component manufacturers must understand every detail of automotive standards, expedite mass production through reliability validation, compare the analysis results of static and dynamic measurements to enhance quality, and master the entire production process from materials to modules.
At the event, DEKRA iST consulting team was on hand to provide professional advice, offering a holistic explanation of our one-stop validation services for wide bandgap power components like Silicon Carbide (SiC) and Gallium Nitride (GaN). The reliability validation solutions comprehensively covers from components to systems, including special high-voltage board design, parameter measurements on power components, and a range of automotive-related reliability tests, such as HTRB, HTGB, H³TRB, and TST.
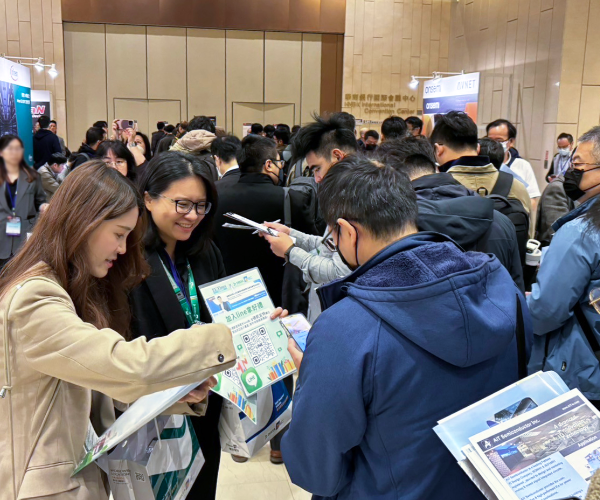
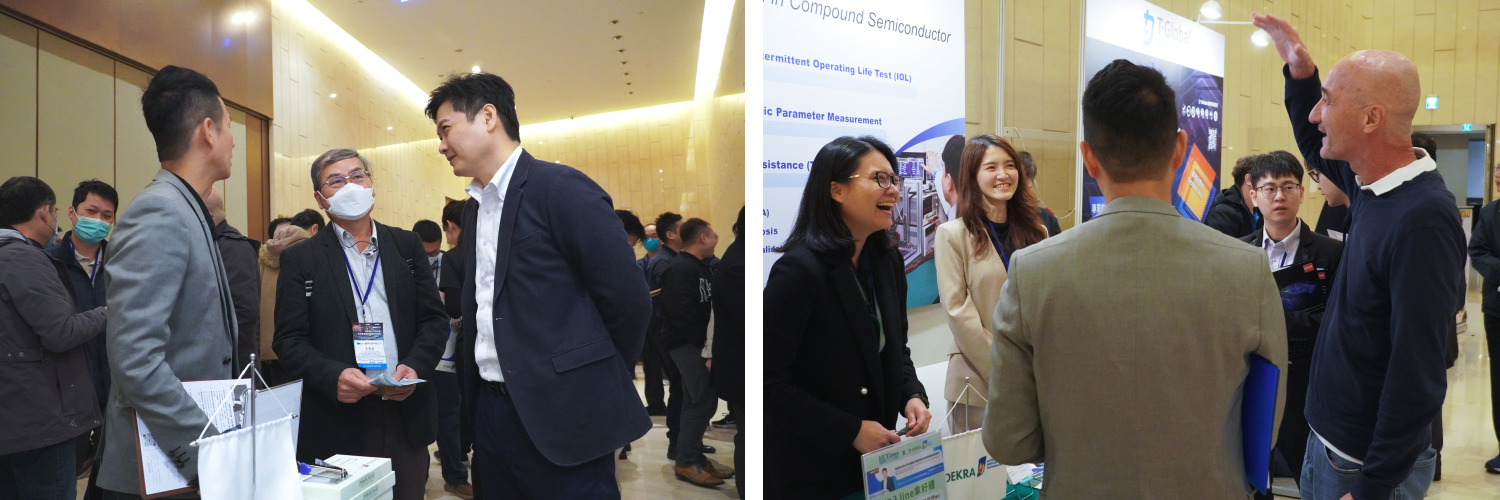
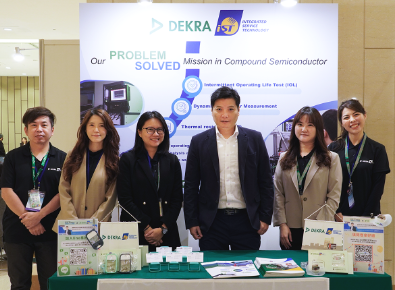
To make all your PROBLEMS SOLVED, we provide professional consultant and service.
For more information or service, please feel free to email to 📧 sos@dekra-ist.com